
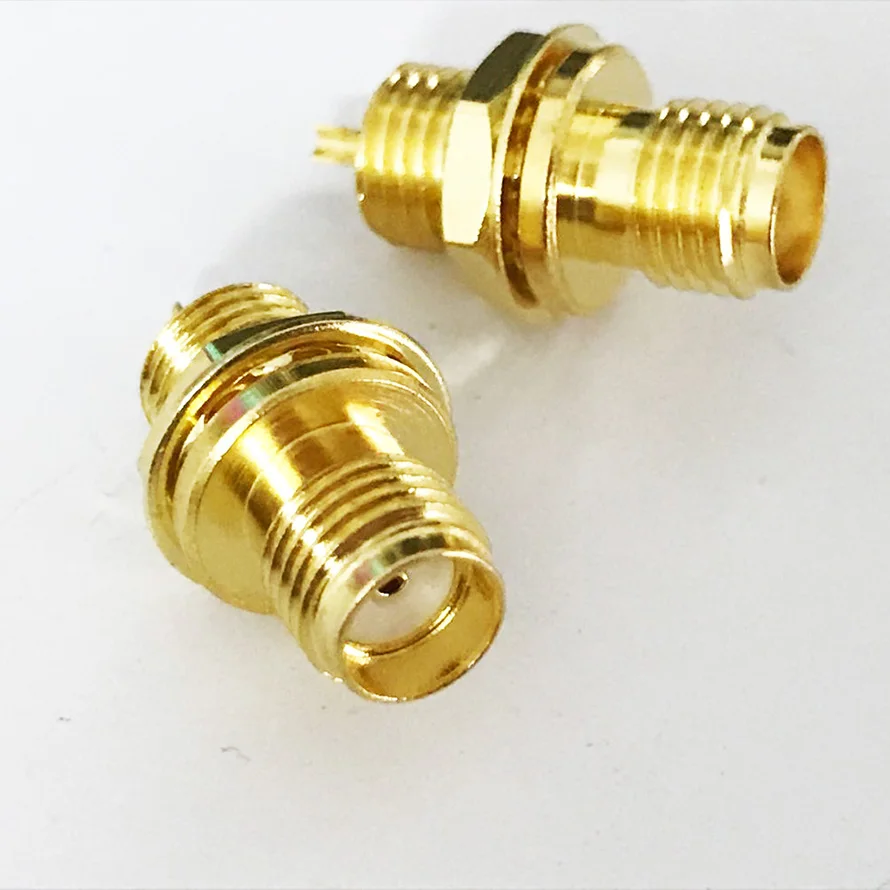
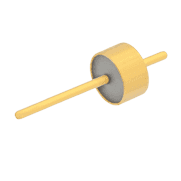
Although this is a standard process on environmentally sealed products, it is incompatible with designs in which contacts are put into place by the customer (crimp contacts). High-quality sealing compounds are used for factory sealing of the block. In this case, the inner contact block of the receptacle must also be sealed to prevent dust or water ingress into the equipment. However, in some cases the waterproof connector must remain sealed even without protective accessories. Normally an open connector should be protected against environmental influences when disconnected, by using an adequate protective cap. Most standard, sealed Fischer Connectors products come with a panel seal. The seal works in a static way in most applications, its exposure to the environment is very limited due to the recessed O-ring position. This sealing element joins the waterproof connector housing with the panel or equipment housing. This seal’s function is to ensure long-term product reliability, especially if the connector is frequently mated and unmated.īecause the interface seal works dynamically when mating, and can be exposed to the environment, you should select the quality of the seal according to operating temperature, environment and fluids. It prevents ingress of water or harmful particles into the connection area where male and female contacts mate.

Our IP68/IP69-sealed and hermetic solutions are available with a wide choice of materials and coatings to ensure their resistance to corrosion, while being lightweight and compact.īy definition, this seal protects the waterproof connector interface, i.e. Salt strongly increases water conductivity, so seawater and salt mist can act as an electrolyte, causing galvanic corrosion. Such demanding applications involved in immersion over long periods require ultra-sealed, watertight, cabled connectors that achieve an IP68 rating in both mated and unmated states. To withstand exposure for extended periods of time in liquids under high pressure, applications such as deep-submarine applications or pipeline-inspection equipment, and seismic-evaluation or drilling instruments in oil & gas, require waterproof connectors with special designs combining hermetic sealing with high-strength mechanical designs to guarantee safe and efficient operations.ĭesign engineers face special technical challenges for their marine and underwater applications such as autonomous and remotely operated underwater vehicles (ROV, AUV or UUV), which operate at depths where diving by humans is either impractical or dangerous. Such connectors should be used in severe conditions like immersion for longer periods of time or exposure to strong water jets. These product ranges, for example, Fischer Connectors’ styles DEE, DBEE, DBPE, etc., are designed specifically for hermetic sealing and undergo a 100% leak test. These applications require a high level of sealing to prevent gas leaks over longer periods of time. Hermeticity is normally required for gas tightness in vacuum applications or pressurized vessels. These products are designed to offer sealing up to IP68. The exposure is generally limited in time and pressure.įischer Connectors’ product range for these applications includes receptacles sealed in mated or unmated states for example, styles DEU, DBEU, DBPU, etc., as well as plugs in association with sealed clamp sets. In typical outdoor applications, one side of the connector might be exposed to rain, dust and other aggressive environments.
